by Dick and Rocky 2003 U320 8/29/10
My auxiliary compressor was running too long and too often. We figured there must be an air leak. We found air escaping from the vent hole on the regulators on both slide manifolds. This regulator looks like this…
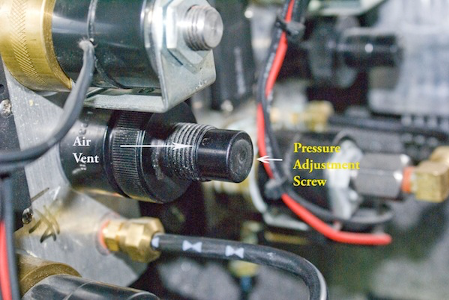
The pressure adjustment screw is painted over to keep you from messing with it. When you unscrew it from the base and remove the brass fitting from within the base, the assembly looks like this…
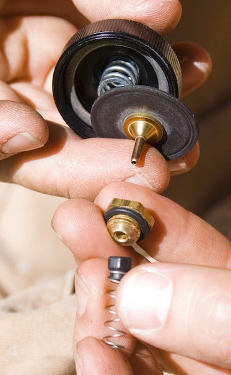
In the photo below, the black rubber piece in the spring on the left has to make two airtight seals. It must seal against the threaded brass fitting and also the tip of the tube extending from the diaphragm.
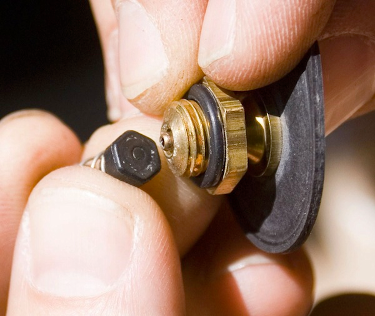
This photo (above) shows two problems; the rubber surface is slightly glazed with permanent circular impressions and there is debris on both the rubber and brass surfaces. We think either or both of these were enough to cause air to bypass the seal, flow through the diaphragm tube and leak out through the vent.
We cleaned off the debris and ran the rubber seal across 600 grit sandpaper about 5 passes. It now looks like this…
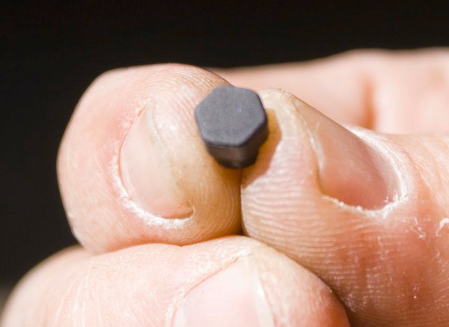
We also cleaned the loose debris from within the base, which looked like this …
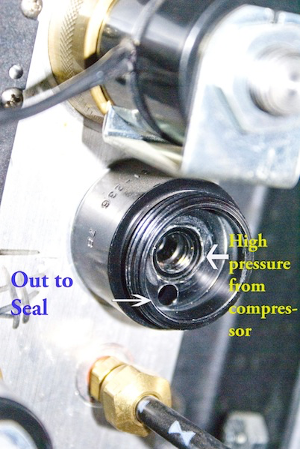
We did this for both slide pressure regulators and it stopped our leak problem. As I type this, the air pressure in this system has dropped from 120 to 110 in about 24 hours. Incidentally, we think that the grooves in that rubber seal also explain why this system would sometimes hold pressure very well (granted that was not often). If the mating surfaces happened to align perfectly with the grooves there was no leak. We actually demonstrated this while troubleshooting.
The following photos are mostly for reference.
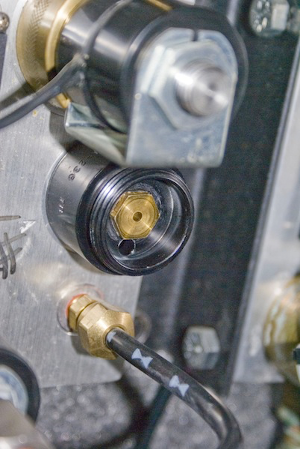
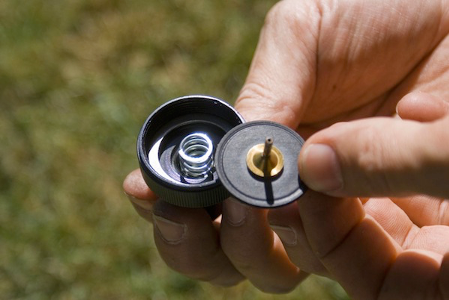
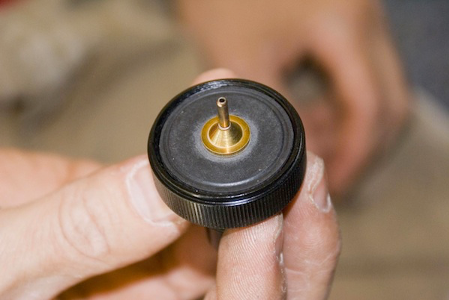
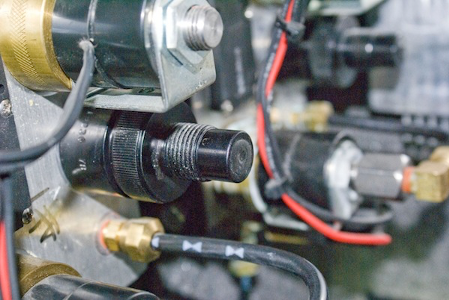
How this regulator works is above my pay grade. My son-in-law explained it to me three times and drew me a picture. I just can’t quite get my head around it. Turns out I don’t have to understand it.